The fundamentals of operations management
Posted on: October 19, 2021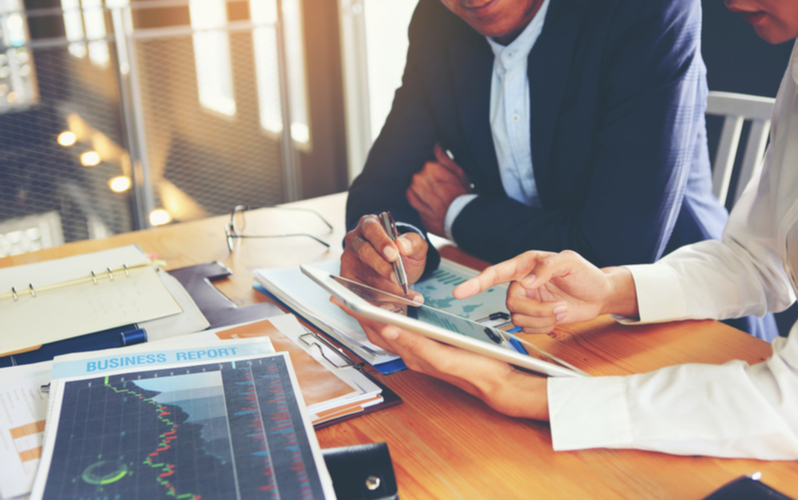
The core tenet of any organisation’s product or service operations is an established, effective operations management strategy.
Operations management refers to the business processes involved with planning, organising and monitoring the production process. It’s concerned with converting raw materials and labour into goods and services in the most efficient manner possible – in short, it aims to optimise the production and delivery process.
From small outfits to large commercial enterprises, businesses which lack the foundations of good operations management are likely to experience issues – including meeting targets. The list is not exhaustive: product quality may suffer; the business may overspend; waste may increase; inefficiencies may become embedded in internal processes; and there may be difficulties delivering to customers on time. Ultimately, the brand may suffer in the marketplace.
Like cogs within a larger machine, individual issues are likely to impact other aspects of the business. To prevent this, leaders must ensure that infrastructure, planning processes and task fulfilment are established and fit for purpose. For businesses aiming to make dramatic improvements in productivity, cycle times and product or service quality, a close look at both operations management and operations strategies is required.
What are the components of operations management?
There are various elements involved in the smooth running of operations – from the early strategic planning stages right through to supply chain management.
According to PlanetTogether, specialists in global operations planning and scheduling, there are 12 main components:
- Forecasting: Here, historical data, facts, figures and statistics are used to make decisions regarding production. This essential step informs how much of a specific product should be produced, aiming to avoid excess inventory or stock shortages.
- Location strategies: Selecting the right location for an organisation’s operations is key as it can impact procurement. For example, the location of a manufacturing facility may be based on availability and proximity to specific materials or skilled labour resources. Transportation costs can also be a factor. Organisational requirements, values and goals will help to determine the appropriate location in order to minimise costs and potential risks.
- Maintenance: Machines and equipment require regular, scheduled maintenance checks. Proper, routine maintenance creates a safer workplace for employees and reduces the risk of unexpected breakdowns and failures that could affect production schedules and quality. Additionally, maintenance ensures machines operate at maximum efficiency for the longest time, ensuring overall production output remains high.
- Purchasing: This aspect ensures that enough raw materials are available to supply incoming customer demand for products. With centralised purchasing, a single department organises purchasing for an entire organisation, whereas decentralised purchasing refers to departments who organise purchasing for their individual needs. Businesses may also use a combination of these strategies.
- Scheduling: This involves assigning jobs or operations to the correct machine or labour resource.
- Total Quality Management (TQM): TQM creates a customer-focused organisation which aims to improve all company activities to meet customer requirements. It focuses on optimising processes and working towards zero defects.
- Materials Requirement Planning (MRP): MRP ensures a business receives the correct amount of each specific material on time in order to meet production targets. It involves taking inventory of current items, identifying whether additional materials are required, and scheduling production or purchase of these materials.
- Quality control: It is important for businesses to conform to product specifications, both for compliance and safety and in order to maintain positive relationships with customers.
- Just-In-Time (JIT): JIT is the process of scheduling operations so that they can begin and end ‘just-in-time.’ It ensures that the number of in-progress items are limited in order for materials and intermediates to progress along the workflow, and avoids bottlenecks and storage of large quantities of in-progress items.
- Process and system performance: Through examination, capacity utilisation and production, businesses can analyse and compare the expected time and quantity of items produced to the actual values. This helps to identify whether a production facility is meeting or falling short of its targets.
- Layout of facilities: This component ensures that the most optimal workflow is established in a production facility. Lean manufacturing – originally developed by the Toyota Motor Company – is the term given to production processes where there is no waste and where any elements that do not add overall value to the finished product are removed. It focuses on seven areas of waste; one is the unnecessary movement of items throughout the facility, caused by poor workflow, poor layout and inconsistent working methods.
- Inventory management: Keeping track of inventory levels ensures that a company is carrying the products needed at particular times and helps to meet demands.
In order for all of these components to function seamlessly, ongoing commitment at all levels of the business – including managing directors, operations managers, business strategists, human resources and a wide range of other team members – is crucial.
Businesses will often benchmark their operations against industry standards, metrics and best practices in order to identify any processes which require improvement. This may result in Business Process Re-engineering (BPR) – rethinking and redesigning core business processes to achieve significant improvements.
Increasingly, technology and information systems have been pivotal in automating processes in a bid to make them more efficient.
Benefits of effective business operations
There are internal and external benefits to strategic business operations planning.
A well-planned, well-executed operations function – including its strategy and schedule – allows a business to decrease overall production turnaround, enabling greater production of goods and timely shipping. This will increase revenue and help to gain, or maintain, competitive advantage in the market. Leaders who succeed in establishing workable business operations also create a scalable systems framework, supporting future expansion and growth.
As well as improving overall efficiency, product and service quality will also improve. This will not only benefit compliance initiatives; higher quality products that reach consumers within quicker timeframes will lead to increased customer satisfaction. Cost-savings from the lean manufacturing process could potentially lead to customer savings, as well as greater profit, which will boost a brand’s profile.
Plus, a safer working environment, underpinned by responsible operations management, will boost employee motivation and retention.
What are operations strategies?
An operations strategy is an action plan which reinforces the operating of a successful business. Based on a series of management-led decisions, it defines an organisation’s operational structure and production capabilities and is governed by the end goal: maximum efficiency and competitiveness.
According to Indeed, common operations strategies adopted by businesses include:
- Corporate strategy
- Customer-driven strategy
- Core competencies strategy
- Competitive priorities strategy
- Product or service development strategy
- Cost-driven strategy
- Outsourcing strategy
- Flexibility strategy
The driving force to any strategic planning is understanding how a business can reap maximum benefits based on its distinctive competencies.
Choosing the most suitable approach will require revisiting previous decisions regarding existing structures and capabilities, reviewing the competition, and assessing aspects such as facilities, human resources, available capital and technologies. It will also depend on the company’s wider goals and the motivations and desires of its shareholders.
The future of operations management: Embracing sustainability and advanced process improvement
Operations management is evolving rapidly, with a strong emphasis on sustainability and advanced process improvement techniques such as Six Sigma. As environmental considerations become more critical, companies are integrating sustainability into their core production planning processes, reducing waste and optimising resource use. Courses covering the fundamentals of operations management are increasingly focusing on sustainable practices, preparing future managers to balance economic efficiency with environmental responsibility. Implementing these principles in inputs, outputs, and logistics will allow companies to meet regulatory requirements and satisfy customer expectations for environmentally responsible business practices.
In the future, capacity and production planning will be heavily influenced by digital tools, data analytics, and flexible learning formats within management courses. These courses aim to equip professionals with knowledge on implementing effective capacity planning strategies to manage demand fluctuations and enhance adaptability. As companies strive for greater efficiency, managers will rely on data-driven insights to refine workflows and improve product quality. This shift not only builds a foundation for operational excellence but also provides a competitive edge as organisations become adept at responding swiftly to market changes.
Upskill yourself in operations management
If you’re interested in developing as a business leader and gaining the management tools to optimise complex business processes, choose Keele University’s online MBA programme.
Learn how to lead from the front in an ever-changing global business environment. You’ll explore digital transformation, project management, organisational and management strategy, sustainable and innovative practice, marketing, human resources management, strategic decision making and much more.